While at RAPID+TCT, we learned that the world of automotive 3D printing had taken a major step forward. To address an immediate supply chain issue, General Motors Company (GM) turned to 3D printing. To produce 60,000 parts over the span of five weeks for use on approximately 30,000 vehicles, GKN Additive, through its Forecast 3D operation, leveraged HP's Multi Jet Fusion (MJF) polymer additive manufacturing (AM) technology.
That is an impressive feat, to say the least. It also marks an historic moment in the history of additive. To learn more about the project, as well as GKN's 3D printing division as a whole, we spoke to John Dulchinos, President of GKN Additive.
3D Printing for GM's New Vehicles
So far, HP's MJF process has been used to produce over 100 million parts. Much of that work is performed by service bureaus and digital manufacturers that rely on the technology for its predictable serial 3D printing capabilities. And among those digital manufacturers is GKN Additive, one of the largest users of MJF in the world. Dulchinos pointed out that, before it was purchased by GKN in 2019, Forecast 3D was actually one of the earliest adopters of MJF.
Some five years later, and we now know that MJF is one of the few polymer 3D printing processes capable of delivering end parts in large batches. Proving this point is the work that HP has done with GM so far. The largest automaker in the U.S. and second largest in the world, GM has used MJF to 3D print heating, ventilation, and air conditioning (HVAC) ducts for its Cadillac V-Series and cooling ducts for the Corvette C8.
These were planned additions, however. For all intents and purposes, GM had no initial intention of squeezing 60,000 3D printed parts into 30,000 vehicles. However, when its design team made a late change to the spoiler of one of its most popular full-size SUVs, it turned to GKN Additive to produce some necessary components with 3D printing.
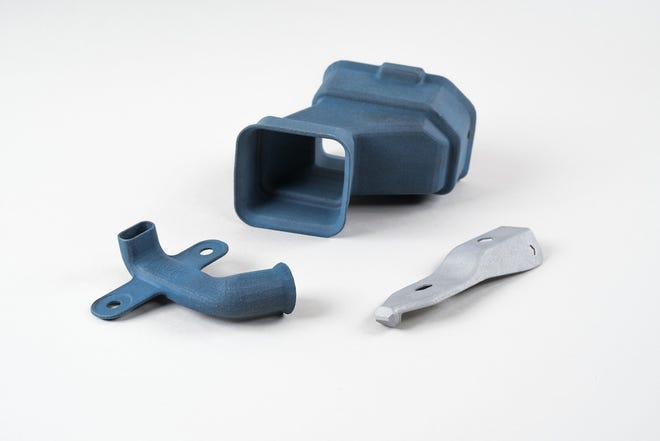
HVAC ducts and electrical harness bracket 3D printed for the V-series. Image courtesy of GM.
First the GM team designed and validated the 3D printed spoiler closeout seals, before ramping production. The digital manufacturer tested and validated the parts, while also implementing a new drying process that cut the time it would have taken GM to surface finish the part in half.
"GM had to make a design change for the spoiler to update it for new standards on fuel efficiency," Dulchinos told a group at RAPID+TCT. "The vehicle was already on the production line when they realized they had to make a change to this tiny seal, but that seal reduced the drag enough that it affected the emissions and fuel economy of the vehicle. So, they had 30,000 of these SUVs sitting in parking lots waiting for this seal. And the tooling for the injection mold was going to take 12 weeks to deliver. So they came to us and we worked with HP, GM, AMT, and BASF to create a solution and deliver 60,000 of these seals in six weeks. That allowed them to get the cars off the lots and to their customers. The 3D printed part was pennies of the total cost, but without it, they couldn’t ship the product."
In particular, I was concerned about the safety implications of implementing a design change to a vehicle so late in the game. Dulchinos assured me that this wasn't an issue for the minor component.
"Well, this wasn't a safety-critical component and it was engineered from a very similar material [to the injection molded counterpart], which was a TPU, and went through very similar post-processing to get to the finished state. From a chemistry standpoint it was all very similar," Dulchinos said.
One issue to the production process was scaling up a TPU part quickly, given the difficulty of dealing with such an elastomeric material, as well as how to post-process the part.

3D printed rear spoiler closeout seal for General Motors, before (left) and after (right) undergoing the finishing process. Image courtesy of GKN Forecast 3D.
Rapid Response 3D Printing
With the ability to turn around a part so quickly for a key manufacturing giant bodes well for GKN and automotive 3D printing going forward. With an "emergency" component now on 30,000 vehicles that will be hitting the roads with consumers behind the wheel, GKN can likely move onto other end parts for the sector. The business now has preliminary workflows in place for just such situations.
"What we’re building now is a discipline around agility with quality. That’s really what we’re trying to get to," Dulchinos said.
Founded in 1759, GKN has a history in metal production that dates back to the birth of the industrial revolution. In the 1990s, it built up its powder metallurgy business substantially, laying the groundwork for adopting metal 3D printing over the past decade.
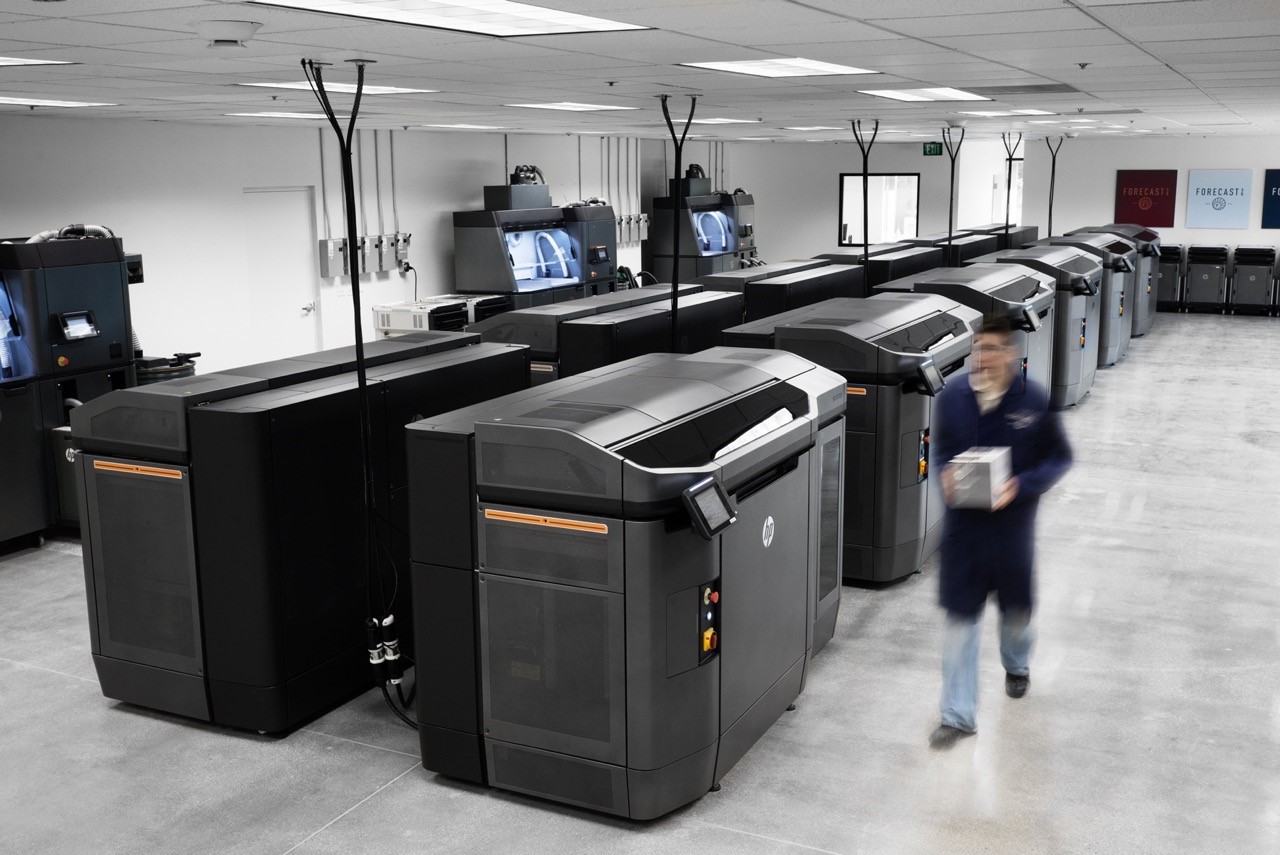
Forecast3D’s early MJF fleet. Image courtesy of GKN Additive.
As a foundational partner for HP's MetalJet metal binder jetting technology, the company has a fleet of four MetalJet machines, which will be scaled up as HP releases the product commercially. It will ultimately be a process for making tens of thousands or hundreds of thousands of metal parts. Additionally, GKN is a leading provider of laser powder bed fusion (LPBF) technology. However, to be a key player in additive services, the company needed a polymer printing business.
"In our traditional business, we make metal powders and then we take that powder, and we make over 12.5 million parts per day. So, it aligns really well with laser- and binder-based metal 3D printing, Dulchinos said. “We also understand serial production super well. What we didn't have initially was a rapid response, digital prototyping service. So, in 2019, we acquired Forecast3D."
Dulchinos went on to explain that every day, he receives a report that lists the current orders, which range anywhere from $25 to $50,000+, but are all processed by GKN Additive daily. This high-mix, high-volume production is the future of additive, according to the company's president. In order to become the agile manufacturer that GKN aims to be, Dulchinos envisions a blend of traditional prototyping jobs with mass production, so that customers can be served across the lifecycle.
"The key is having the digital infrastructure and quality management systems to make this work. When I make a plastic prototyping part, the quality requirements are pretty basic. No one’s asking me to make sure that this is down to a 10th of a micron in precision. They’re really not concerned with, say, how flat it is or what the texture is. They just want it fast. But we do that at scale. In Carlsbad, we run a highly disciplined manufacturing process with over 40 HP MJF printers, making prototyping parts at scale. Then we've got a host of other applications where we’re in production, using the same manufacturing discipline but to a much higher level of quality," Dulchinos said. "I think the future state of 3D printing is going to be a blend of the two. It’s going to require digital agility but at scale. We have to deliver that with quality systems and the process rigor that comes from GKN's proven, agile processes."
From Parts to Solutions
Dulchinos joined GKN Additive in 2022 by way of Jabil, another manufacturing solutions provider that, in many ways, overlaps with GKN's own additive activities, down to the use of MJF printers. Having previously served as Vice President of Digital Manufacturing at Jabil, Dulchinos was a prime candidate to lead the AM division of GKN.
"They’re both world-class manufacturing companies. So, structurally at the end of the day, both have over long, long periods of time—decades in the case of Jabil and centuries in the case of GKN—building a business around delivering products to customers to solve problems, with very exact standards and consistent quality," Dulchinos said.
"I think the fundamental difference between the two is that Jabil is more of a systems provider whereas GKN is more of a components provider. Ultimately, Jabil could make or buy a part based on the value around the solution. In some cases, it may make sense to go down to the component level, but Jabil's core competency around supply chain management encompasses the broad set of components. GKN's core competency is in actually manufacturing parts."

3D-printed copper induction coils from GKN Additive. Image courtesy of GKN Additive.
Dulchinos says that now, GKN is in the process of transitioning from being a parts business to a solutions business dedicated to specific verticals, applications, and customers. This is demonstrated by the fact that GKN offers additive solutions for such unique applications as copper inductors and heat exchangers. Explaining his philosophy to the business, Dulchinos concluded:
"3D printing has been around for a long time. The problem I see with it is that we need to move beyond selling technology to enabling solutions. Everyone's got the latest technology they want to showcase, but for this to move to the kind of growth numbers that have been modeled, it needs to move from a technology to a manufacturing solution. To do that, there needs to be a thought process about enterprise-level solutions, not just making parts. I think it’s great to have companies like HP in the game. We need Fortune 100 companies in this space thinking about enterprise-level solutions. That’s really what GKN offers. We’re the enterprise-level solution for manufacturing. Ultimately, that is what the large OEMs are going to want to see. They want a real supply chain and real supply chains require companies with really deep manufacturing pedigrees and healthy balance sheets so that we can support that kind of growth."
Feature image courtesy of GKN Additive.
The post 3D Printing for GM SUV Opens Doors for GKN Additive’s Flexible Manufacturing appeared first on 3DPrint.com | The Voice of 3D Printing / Additive Manufacturing.