It’s another busy week of events and webinars coming up, starting with the AM Industry Summit in Long Beach. 3D Delta Week and the Silicone Expo are also taking place, and Velo3D takes its Seeing is Believing tour to Germany and Japan, while Stratasys continues to travel the U.S. with its Experience Stratasys tour. Webinars will cover metal 3D printing, 3D printing Hollywood props, Materialise Magics software, and more.
June 18 – 21: ASME Annual Meeting

First up, ASME is holdings its Annual Meeting in Scottsdale, Arizona; it started yesterday and ends on Tuesday, June 21st. Held at the Fairmount Scottsdale Princess, the meeting is a way to celebrate the major developments of members and honor outstanding contributors. A few special events will take place, including a Ralph Coats Roe lecture on Sunday, followed by the opening reception that night. The business meeting will be on Monday afternoon, and that night, the ASME Leadership Celebration will be held.
“The ASME Annual meeting provides a forum for ASME members and other engineering professionals to assemble for personal and professional growth, to meet with other members and exchange information on how they are dealing with common challenges and learn about trends and developments affecting the future of the profession.”
If you’re an ASME member, you can register for the Annual Meeting here.
June 20 – 22: AM Industry Summit

If you’re in Long Beach, California this week, you don’t want to miss ASME’s AM Industry Summit, June 20-22. This event, created by engineers for engineers, is a hybrid one, so you can attend virtually as well. Focused on leveraging 3D printing capabilities within the aerospace and energy industries, the conference includes three days of technical sessions and keynotes across three tracks, a hands-on Technology Showcase, and an exhibitor hall. Attendees will have the chance to network with hundreds of cross-industry AM engineers, manufacturers, product designers, and technology professionals about everything from materials to quality and processes.
“AM Industry Summit brings together the global additive manufacturing aerospace and energy industries for a unique, hands-on interactive event. Discover the latest materials, metals, and polymers, while uncovering design and technology solutions across the AM and 3D printing industry.”
You can register for the summit here.
June 20, 21, & 23: Velo3D’s Seeing is Believing in Japan & Germany
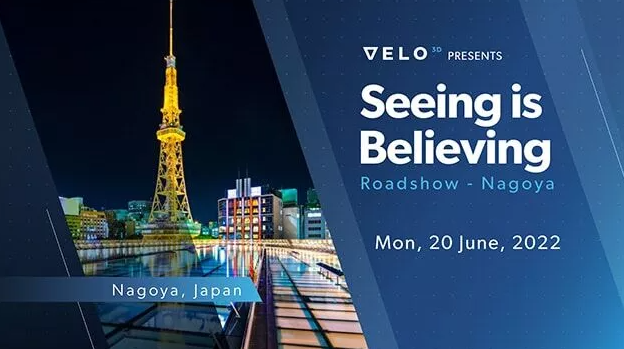
This week, Velo3D is bringing its Seeing is Believing Roadshow to Japan and Germany. On Monday, June 20th, the tour goes to Nagoya, Japan, and then to Augsburg, Germany on the 21st. On the 23rd, there will be two sessions in Tokyo. These tours are a great opportunity for visitors to learn how Velo3D's end-to-end AM solution is pushing the boundaries of what the technology can achieve in important industries like aviation, space, oil & gas, and energy. The presentations will highlight Velo3D’s process all the way from design and printing on the Sapphire XC system to quality assurance and post-processing, and attendees will get to see real-world examples of parts printed by customers.
“When we talk to prospective customers who have experience with additive manufacturing, the first thing they want is to see the parts for themselves to witness whether the geometries we offer can truly be achieved. In our pilot of the Seeing is Believing roadshow we made amazing connections between engineers, technology influencers, and executives in the additive manufacturing industry to learn from and inspire one another. We look forward to achieving this same community building in Europe,” said Renette Youssef, Velo3D CMO.
June 20, 21, 23, & 24: The Experience Stratasys Tour Continues
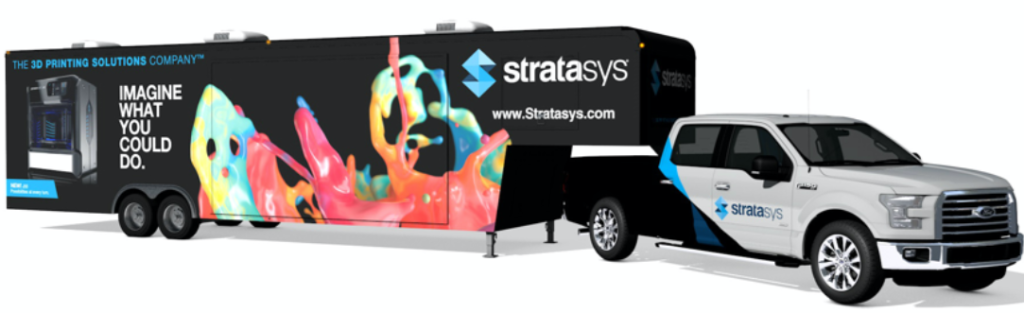
This week, Stratasys continues its Experience Tour in the Midwest, starting at Pinstripes in Oak Brook, Illinois on June 20th. The tour moves on to CATI HQ in Buffalo Grove, IL on the 21st, and then moves on to Indiana. On June 23rd, Stratasys will be at the Boathouse Restaurant in Winona Lake, IN, and then at Upland Brewing in Columbus, IN on the 24th. CATI will be hosting all four of these stops.
"Our mobile showroom offers a local, convenient way for you to talk with 3D printing experts and see the latest 3D printers, materials and solutions from Stratasys. Learn about additive manufacturing services from Stratasys Direct and discover how your organization can benefit from 3D printing applications."
You can register for the Stratasys Experience Tour here. Stay tuned for more dates and locations in the future!
June 20 – 24: 3D Delta Week (3DDW)

Next up, from June 20-24, the first edition of the 3D Delta Week (3DDW) events series is taking place in the Benelux (Delta) region, specifically Belgium and the Netherlands. Organized by Brainport Eindhoven, Flam3D, Mikrocentrum, and Jakajima, the week is meant to be immersed in 3D manufacturing, including PLM, software, VR, 3D printing, model-based definition, VR, and more. According to the founders, the Benelux Delta is “a top region in terms of 3D printing,” with many promising startups and lots of academic and applied research going on, but the region’s AM ecosystem needs a better podium. 3D Delta Week involves several 3D manufacturing-centric events, including Additive Manufacturing R&D Day, a masterclass in scalable production for high-volume AM healthcare applications, the Materialise Open House: VIP Day, and the 3D Delta Dinner, and attendees can put together their own program.
“3D Delta Week creates value for users and providers along the 3D Manufacturing Value Chain. It is the 3D manufacturing meeting point for expert and layman, inside or outside the Benelux region.”
June 21 – 22: HI-AM Conference
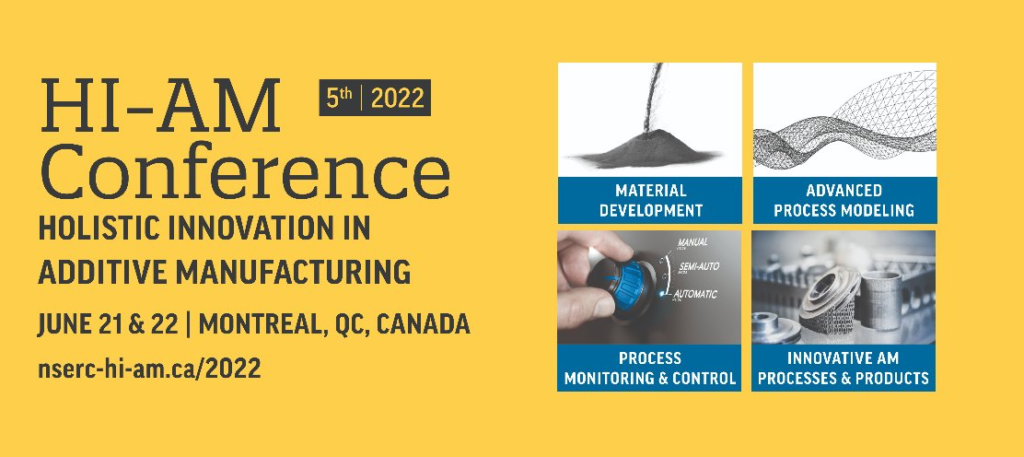
The 5th annual gathering of the NSERC Network for Holistic Innovation in Additive Manufacturing will be held from June 21-22 in the form of the HI-AM Conference, the only academic conference in Canada that’s focused solely on metal 3D printing. Co-hosted by McGill University and the University of Waterloo, HI-AM 2022 will be held in Montréal and welcome hundreds of AM experts and decision-makers from research institutes and academia, government, and industry to disseminate and discuss AM research results with HI-AM Network members and the scientific community. The main conference features will be keynote speeches, oral research presentations, and poster presentations
“The focus of HI-AM Conference is to provide a platform for the presentation of recent R&D advancements in the field of metal additive manufacturing under 4 research themes: (1) material development, (2) advanced process modeling, (3) process monitoring and control, (4) innovative AM processes/products.”
You can register for HI-AM 2022 here.
June 21 – 23: Silicone Expo USA

If you’re part of the manufacturing or extended silicone supply chain of elastomers, fluids, resins, or gels, you don’t want to miss Silicone Expo USA, taking place from June 21-23 at Huntington Place in Detroit. This free, one-stop-shop for all things silicone will feature over 100 exhibitors displaying a range of services and products that support silicone applications in many fields, including automotive and medical, in addition to more than 28 sessions and over 35 speakers. The two track conference and trade show will also offer networking opportunities, international exhibitors, thought leadership discussions, the chance to learn the latest industry developments, and more.
“Industry peers from around the world will be providing key insights, innovation, R&D, education and thought leadership discussions for one of the world’s most important and adaptable materials.”
You can register for the expo here.
June 21 – 23: SPEE3D at CSAT & LSAAT
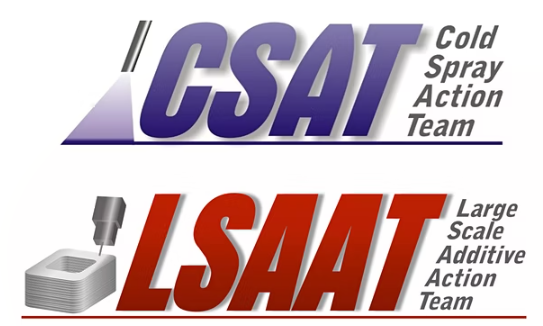
The Cold Spray Action Team (CSAT) 2022 meeting is delivering a two-day hybrid session on June 21st and 22nd, while the inaugural Large Scale Additive Action Team (LSAAT) conference meeting, which is an in-person extension of CSAT 2022, will be on the 23rd, and SPEE3D will be at both of them. The theme of CSAT 2022, which will be held both virtually and at the DCU Center in Massachusetts, is “Cold Spray Additive Manufacturing or CSAM,” and will feature several topics, including machine learning, feedstock powders, non-destructive testing, cold spray at the point of need, and, of course, 3D printing. LSAAT 2022 will be at nearby Polar Park, and offer a community platform to discuss large format Solid-State and Direct Energy Deposition (DED) AM processes like Laser, Electron Beam and Plasma, Wire Arc, Friction Stir, and Cold Spray.
“With the successes of cold spray technology continuing to build, we are excited to once again bring the CSAT Meeting to the cold spray community. Scheduled for June 21 & 22, 2022 back again in the heart of Massachusetts with an additional extension day for wire arc additive manufacturing and friction stir additive manufacturing on June 23, 2022 introducing the Large Scale Additive Action Team (LSAAT); this event promises to be our biggest yet with more applications, exhibitors, and new commercial success stories than ever before.”
You can register for the CSAT + LSAAT 2022 Action Team Meetings here.
June 21: Tools to Implement AM with GE Additive

At 10 am EST on Tuesday the 21st, GE Additive is holding a webinar on “Beyond the Machine: Tools Needed to Successfully Implement Metal Additive.” The presenter, GE Additive Project Manager Halima Iqbal, will look into the available ancillaries for achieving success in metal AM, and also introduce the available capability packages for the company’s M2 Series 5 DMLM printer, which can be customized to a customer’s specific needs.
“Metal additive manufacturing offers numerous benefits for producing innovative parts, whether you intend to use the technology for prototyping or low-scale production or full industrialization. While important, the metal additive machine you select is only part of the equation when it comes to implementing additive manufacturing. A variety of tools are necessary to help you achieve success, whether it's software, hardware or qualification assistance. And the tools you need can vary depending on what your manufacturing goals are (prototyping vs. production) and the industry for which you are producing parts (regulated vs. non-regulated).”
You can register for the webinar here.
June 22 & 23: Materialise Magics Training in the UK

Materialise offers training courses throughout the year, both online and in-person around the world. This Wednesday the 22nd, a one-day Magics Update training course will be offered in Bangalore, India, and another one will be held in London on Thursday the 23rd. Attendees will get an update on all the latest features of Magics 26, and learn how to optimize their workflow with the new Part and Platform scenes, how to improve the accuracy of editing operations by introducing BREP functionalities during data preparation, how to use the Sinter Module with fixed height supports for metal binder jetting and EBM, and more.
“Take full advantage of the newest version of Magics with the Magics 26 Update Training. All Materialise Magics maintenance customers are eligible for free online or in-person training sessions to discover the latest updates and features.
“Join this one-day course and significantly optimize your use of Magics 26.”
June 22: Nexa3D Live at HQ

If you’ve ever wanted to see the inner workings of Nexa3D, you’re in luck! At 12 pm EST (9 am PT) this Wednesday, June 22nd, you can virtually visit the team at Nexa3D’s headquarters in Ventura, California. Sarah Goehrke, Senior Director, Strategic Communications and Ecosystems, and Avi Reichental, Co-Founder, Chairman, and CEO, will take you on a live visit for a look around the company’s offices, NextFactory, and its new Customer Success Center.
“Both our team and our product portfolio have doubled over the last year — join us for a look inside and see where the magic happens, meet a few more of those magic makers, and go behind the scenes with Nexa3D.”
June 23: 3D Printing Hollywood Props ultraFAST
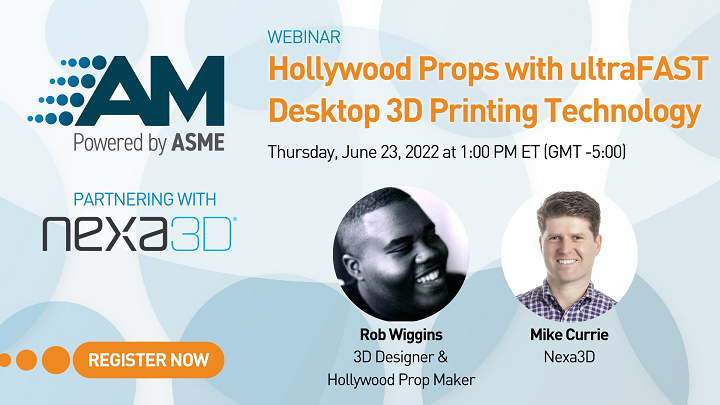
Speaking of Nexa3D, it’s joining ASME this Thursday, June 23rd, at 1 pm EST to discuss how to make “Hollywood Props with ultraFAST Desktop 3D Printing.” Nexa3D’s Mike Currie will talk with Rob Wiggins, a 3D designer and Hollywood prop maker, about how Nexa3D’s ultraFAST AM technology is used in Hollywood to increase throughput and manufacture accurate one-off parts fast and at less cost, how Wiggins designs and produces full-scale props and characters with 3D printing, and the prop maker’s recent discovery of how 3rd generation resin 3D printers can help him print projects in just hours, using a variety of performance materials.
“3D printing is becoming ubiquitous in Hollywood. The flexibility to manufacture one-off parts quickly and cheaply makes the technology an invaluable tool. Rob Wiggins is one such Hollywood prop maker who has worked on the Transformers, Star Wars, and Marvel film franchises as a contractor for Hasbro, as well as designing and producing props and characters for major TV shows and Movies.”
You can register for the webinar here.
June 23: Stratasys Talks Large Geometry Prints with DLP

Also at 1 pm EST on the 23rd, Stratasys will hold its latest webinar, “Overcoming Large Geometry Challenges in DLP 3D Printing.” Marshall Ling, Process R&D Manager at Stratasys, will teach attendees how a programmable print process allows for new applications that were previously nearly impossible due to the inherent challenges of DLP. You’ll also get to see real-world examples that show how the Origin One printer can produce advanced geometries, like smaller densely-nested parts or solid molds.
“A lesser-known challenge for many if not all 3D printing technologies is the ability to print large bulky parts without sacrificing part quality. Whether it be thermal gradients, internal stresses, or throughput hurdles; most 3D printing technologies must overcome at least one of these factors. In the case of DLP printing it's all the above.”
You can register for the webinar here.
June 23: Nondestructive Evaluation Services with America Makes

From 2-3 pm EST on the 23rd, America Makes is holding a TRX Webinar called “Good Vibrations: Process Compensated Resonance Testing for Additive Manufacturing Inspection.” New Mexico-based Vibrant Corporation provides nondestructive evaluation (NDE) services to aerospace, automotive, and power generation maintainers and manufacturers, using a whole-field Process Compensated Resonance Testing (PCRT) inspection to scan a component’s resonance frequencies; then, the data is analyzed with machine learning and statistical analysis tools. Vibrant uses PCRT for parts with traditional forms of manufacturing, as well as additive, and parts with structural flaws will have a different resonance signature. During this webinar, Vibrant will give technical background on PCRT, discuss its work in the America Makes Maturation of Advanced Manufacturing for Low-Cost Sustainment (MAMLS) Program, and provide examples of PCRT applications for additive manufacturing.
“In production testing, the PCRT scan and analysis is performed automatically, requiring no operator interpretation of the results. Inspections with PCRT typically require less than 10 seconds to scan the part and return a Pass/Fail result. The whole field nature of PCRT enables inspection of highly complex part geometries. An America Makes report determined that PCRT is one of only two NDE methods than can inspect the full range of complexity expected in additively manufactured components. Vibrant and PCRT have established a stellar track record of eliminating field failures in critical components. Vibrant's inspection services reduce costs, accelerate customer inspection throughput, and offer statistically rigorous tools for monitoring and controlling production processes.”
You can register for the webinar here.
June 24: TechBlick Innovations Festival for Electronics

Finally, TechBlick, the home of additive electronics, is holding a one-day, virtual Innovations Festival on Friday, June 24th, about Printed, Hybrid, 3D, InMold, and Textile Electronics. The global audience will enjoy more than 55 live exhibitors and 42 speakers, all focused on major electronics advances from around the globe. Topics will include everything from e-textiles, smart packaging, and printed sensors and displays to nano-scale wafer printing, printed batteries and hybrid circuits, perovskites, additively manufactured electronics (AME), and more.
“In this innovation festival, the speakers will present the latest advances and innovations in compact technology-focused 5-min speeches. To continue the discussion, the participants can then visit the speakers in their virtual speaker corner or at their virtual booth.”
You can register for the festival here.
Do you have news to share about any future webinars or virtual and live events? Please let us know!
The post 3D Printing Webinar and Event Roundup: June 19, 2022 appeared first on 3DPrint.com | The Voice of 3D Printing / Additive Manufacturing.