The idea of being antifragile means that you as a person, company, or other system can withstand shocks well and then emerge even better from them. In part one of this series, we looked a little bit into what antifragility means as a desirable characteristic. Here, we’re going to explore whether or not 3D printing can make you antifragile and if the 3D printing industry is antifragile in itself.
3D Printing is Not Antifragile
We’re assuming here that antifragile is something that we would like to be. Can we simply make an organization antifragile by throwing a few 3D printers at it? Is the technology able to transform a company simply through exposure? The obvious answer here is: of course not. Culture, respect, and many other factors will carry the day here. Simply having the box will not change the firms’ brittle response. If you have a top-down organization with management by fear as the main cultural trait, then you could get all the boxes, tick all the boxes, and still be glass when it comes to a shock.
Maybe 3D Printing is Antifragile
However, there could be a more nuanced view here that 3D printers could engender antifragility and make it more likely to occur. We know that 3D printing is a technology that helps one go from idea to file to part quicker than other processes.
Additive manufacturing (AM) can allow businesses to iterate, react and make parts and solutions faster than other companies can. These parts may not solve all problems, but only some. For these limited problems for which AM can make part-sized solutions, our industry can develop skills and methodologies. These skills and methodologies could be honed so that, over time, one could become more antifragile.
With each new crisis, we could identify parts faster, identify problems faster, design parts faster, print them out better, and become more rapid at doing this all in concert. We could make sure that we designed the right parts and printed them out with the right technologies. On the whole then, we would hope that, sometimes, such behavior would lead to more antifragility. We know we cannot 3D print all of the solutions, but, for some, our methodology would help.
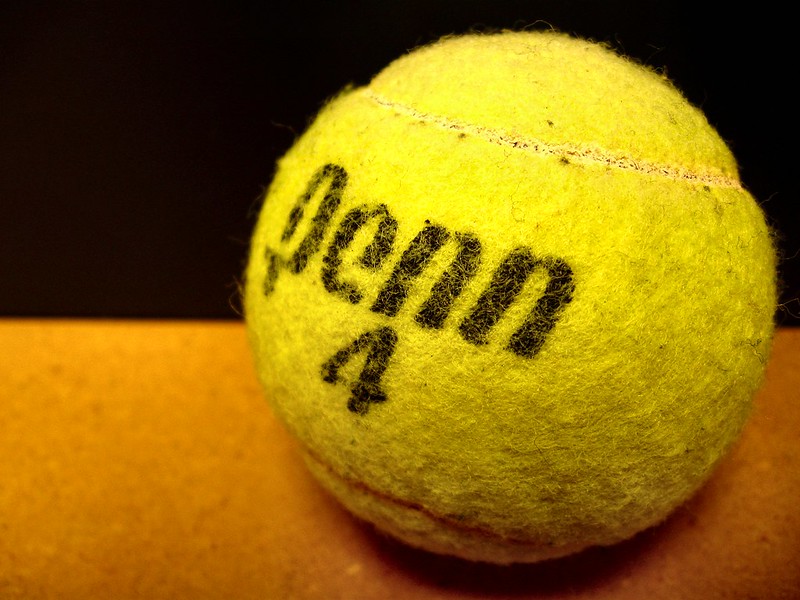
Skunk Works it
I’ve written about 3D printing as a kind of duck tape for businesses. Our technology can help people find solutions faster through improvisational engineering. AM can make more errors more quickly and iterate to a degree that other technologies cannot. This leads to shorter—yet more convoluted—paths to success.
Many companies are process-driven or do not tolerate failure, even in the face of adversity or times of crisis. In many firms, internal politics and power structures obliterate or block paths to the Truth and towards solutions. If we have to get all of the disparate actors to suspend their power struggles to agree on a path forward, it will never happen.
One of the reasons that Skunk Works centers are successful is that they create a sandbox or lab outside the existing organization and its resident politics. Successful Skunk Works are also almost always physically separate from not only the structure of the company but also its buildings in order to let the operation move more quickly there.
In a similar way, a 3D printer can be used as a method to circumvent existing procedures, paths, and institutional competition. By printing, we get a part faster while also avoiding discussions about budget, whose responsibility it is to make a thing, the cadence of the weekly meeting, and much more. In effect, therefore, AM could potentially make a rigid organization more flexible and, in turn, more antifragile. A process-driven and slow organization could become more responsive and faster.
During COVID, some of my clients became much more rapid in their decision-making because everyone was at all scheduled meetings. Their rate of selecting choices increased. This doesn’t mean that having 3D printers could make you antifragile per se, but it could really help. In this case, it wouldn’t be the technology that is making a business more antifragile in and of itself. However, 3D printing can help you sidestep traditional paths and structures to implement change more quickly.
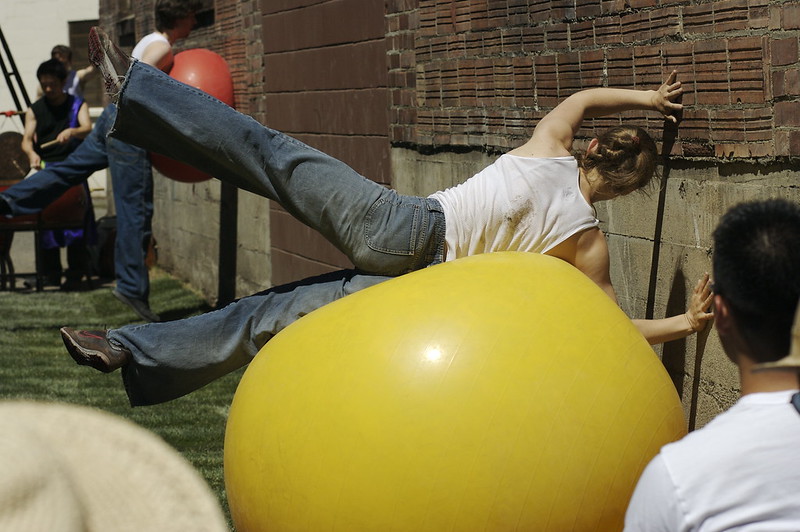
3D Printing is Definitely Maybe Antifragile?
We don’t really know what an antifragile organization looks like. We don’t know how it would act and could consistently respond better to chaos or crisis. But, we could theorize that an antifragile company would need flexible tools that could keep up with its moves. We might assume that whatever antifragile policies and behaviors such a business would have, it would need to be quick and unique—things that AM is eminently good at.
On the whole, however, we can’t really prove that 3D printing would some how make you antifragile. But, we can assume that a company with 3D printers would be more inclined to implement the hardware portion of any improvisational hardware solutions that they may need.
Images: Michelle Hofstrand, Joe Silagyi, Helen Cook.
The post Can 3D Printing Make You Antifragile? An Argument for Skunk Works appeared first on 3DPrint.com | The Voice of 3D Printing / Additive Manufacturing.